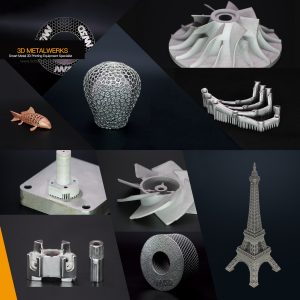
3DMETAL WERKS has its own core technology!
1. Adjustable parameters: Parameters can be adjusted according to the actual needs of customers to achieve the best printing effect. 2. Joint research and development: Jointly develop the application of various new materials with customers, and customize the best product full set of solutions. 3. High printing accuracy and good stability: Precision parts are imported products,